Зварювання металів з'явилася із зародженням кування. Поява все більш складних механізмів вимагало вдосконалення технологічних процесів кування і зварювання. З'єднання окремих деталей в цільні вузли куванням - процес складний і трудомісткий, але до появи зварювання за допомогою електричної дуги був єдино можливим.
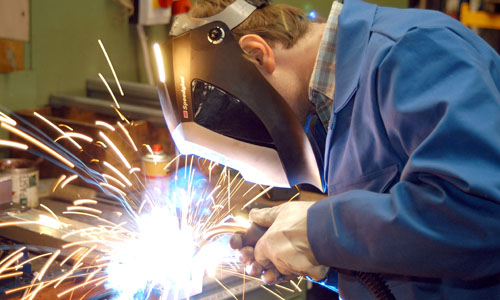
Зварювання є найпростішим і міцним способом з'єднати різні деталі з металу.
В даний час вже розроблено понад 150 способів дугового зварювання, і напрацювання нових технологій тривають.
Основні види зварних швів
Відрізок з'єднання, сформований в результаті процесу кристалізації розплавленого металу, прийнято називати звареним швом. Однією з головних характеристик зварних з'єднань є катет зварного шва.
Існує два види зварних швів (не плутати зі зварювальним з'єднанням):
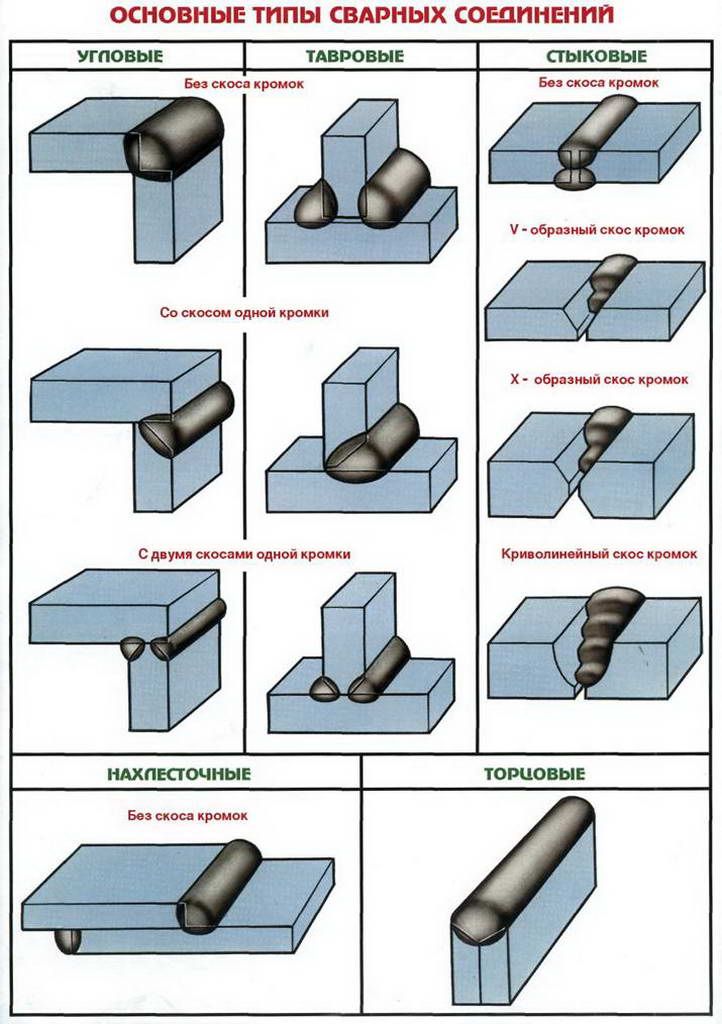
Основні типи зварних з'єднань.
- Стикові зварні: застосовуються для з'єднання встик, тобто деталі з'єднуються торцовими краями. З'єднання встик проводиться без оброблення крайок, з обробленням і з відбортовкою краю деталі. Краї можуть мати криволінійну форму, V-образну і Х-образну. Листи до 8 мм можна зварювати без оброблення крайок, але потрібно листи укладати з зазором до 2 мм. У практиці стикові варіанти частіше застосовуються для з'єднання трубопроводів і при виготовленні конструкцій з листових металів. Такі сполуки найбільш економічні і менш енерговитратні.
- Кутові: бувають власне кутові, таврові і нахлесточного. Оброблення кромок може бути одно- і двостороння, в залежності від товщини металу. Кут оброблення вибирається від 20 ° до 60 °. Однак потрібно враховувати, що більший кут оброблення вимагає більше металу для заповнення, значить, знижується продуктивність і якість.
- Електрозаклепочная зварювання застосовується для обшивки великих конструкцій тонколистовим металом. Застосовують, наприклад, при виготовленні пасажирських вагонів, коли застосування суцільних швів утруднено і нерентабельно. Електрозаклепочние з'єднання виходять досить міцними, але не щільними.
Зазвичай зварювання виробляється за один раз, але якщо товщина зварюваного металу не дозволяє проварити матеріал, проводять в декілька заходів. Такий метод називається багатошаровим. У цьому випадку кожен попередній шар віджигається наступним, в результаті такого термічного впливу значно поліпшуються властивості і структура шва.
Вибирати вид з'єднання потрібно в залежності від конфігурації виконується елемента конструкції. Кінцеве виріб повинен бути працездатним, переносити розрахункові навантаження і не піддаватися втомним руйнуванням.
Переваги зварювальних з'єднань:
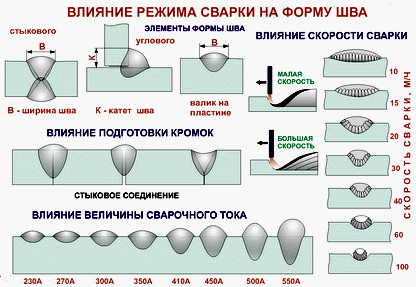
Вплив режиму зварювання на форму шва.
- Невелика трудомісткість і простота виконання з'єднання.
- Невелика, в порівнянні з іншими видами з'єднань, гучність процесу.
- Можна легко автоматизувати процес.
До недоліків можна віднести можливість залишкових напруг і ненадійність в роботі при вібраціях і ударних навантаженнях.
Властивості і геометрія зварних швів
У всіх конструкціях є робочі шви, які сприймають основні навантаження. Розрахунки на міцність робочих швів проводяться на повне навантаження плюс 25%. Для з'єднання окремих елементів використовуються сполучні шви - вимоги до них не такі жорсткі, тому що в разі їх руйнування робота конструкції не буде порушена.
На якість зварних з'єднань впливають багато чинників: здатність матеріалу створювати монолітний шов, присадки і флюси, окислюваність металу, положення шва: горизонтальне, вертикальне, похиле або стельове.
Властивості зварного шва визначаються в основному його геометричними розмірами.
Загальні геометричні параметри:
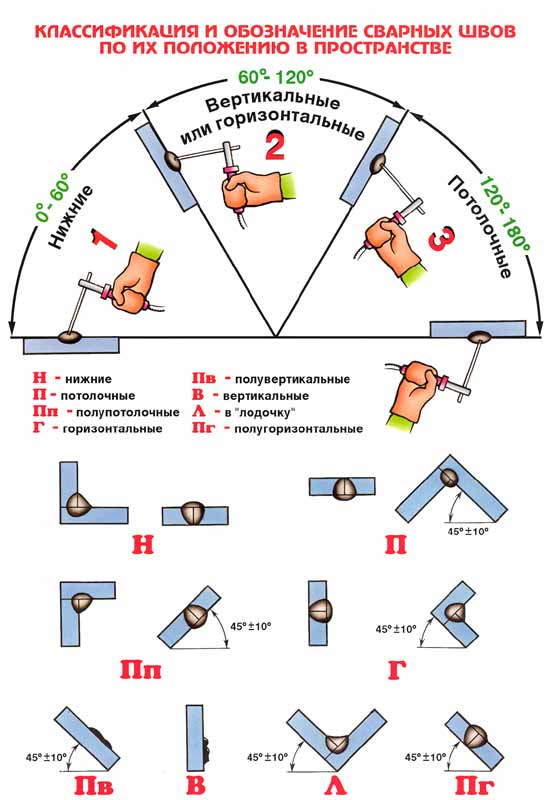
Класифікація та позначення зварювальних швів.
- Ширина - відстань між кордонами сплаву.
- Увігнутість (опуклість) - відстань між лінією і основним металом, і поверхнею, візуально проходить по лінії максимальної угнутості (опуклості).
- Корінь - сама нижня частина.
Для кутових з'єднань характерні ще такі величини: наявність катета зварного шва, товщина, опуклість і розрахункова висота.
Катет кутового шва - це катет найбільшого рівнобедреного трикутника, вписаного в поперечний переріз. При зварюванні заготовок однакової товщини катет може здаватися по кромці, при різній - його ставлять по товщині більш тонкого матеріалу. Розмір катета повинен забезпечувати міцність з'єднання, але надмірне збільшення його може викликати деформацію вироби.
Має значення форма поверхні зварного шва: опукла, увігнута або плоска. Шви з опуклою поверхнею - посилені - краще працюють при статичних навантаженнях. Увігнуті поверхні - ослаблені - краще витримують динамічні навантаження. На практиці частіше застосовуються шви з плоскою поверхнею як більш універсальні.
додаткові характеристики
Форма поверхонь швів безпосередньо залежить від застосовуваних електродів.
Крім загальних вимог до всіх випускається електродів (стійке горіння дуги, певний хімічний склад металу шва, відсутність розбризкування і т.п.), пред'являються ще й спеціальні вимоги. До таких відноситься отримання шва заданої форми. Електроди, розплав яких дає густу в'язку масу легко формують опуклий шов.
Вибір електродів проводиться за технічними характеристиками, вказаними на кожній упаковці відповідно до технічних умов, заданими в проекті.
На властивості і геометрію зварного шва впливає режим зварювання.
Зі збільшенням сили струму збільшується глибина провару при незмінній ширині шва. При збільшенні напруги різко збільшується ширина шва з подальшим зменшенням глибини провару. Зі збільшенням швидкості руху електрода до 50 м / ч ширина шва зменшується, а глибина провару збільшується. Збільшувати швидкість більше 50 м / ч нераціонально, тому що можуть з'явитися підрізи внаслідок слабкого прогріву основного матеріалу.
Якість з'єднань проводять двома способами: руйнують і неруйнуючих контролем.
Неруйнівний контроль дозволяє виявити зовнішні дефекти за допомогою спеціальних зварювальних шаблонів, внутрішні - з допомогою ультразвуку, рентгенівським просвічуванням і гаммаізлучателем.
Ти, що руйнуєш контроль проводиться свердлінням, випробуванням міцності на розтягнення, вигин, ударну міцність з руйнуванням зразків.